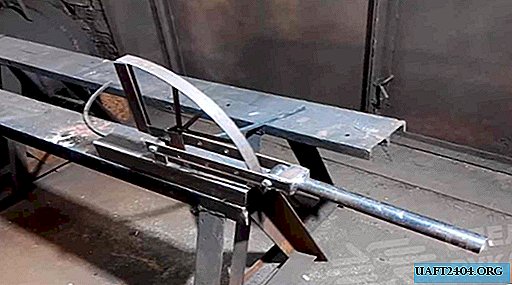
In this review, the author shows the manufacturing process of a home-made manual machine.
With its help it is very convenient to make arcs and half-arches from a profile pipe, strip, round timber and square.
For the manufacture of the machine, the author uses trimming profile pipes 60 * 60 mm, several strips, a piece of pipe with a diameter of 25 mm.
Also, for the manufacture of other parts, bolts with nuts and washers with a diameter of 10 mm will be required.
First of all, the author notes pipe segments 6 cm and 4 cm long, and cuts off the workpiece with a grinder.
The main stages of work
At the next stage, we put a washer and two nuts on the bolt. First, we weld the nuts together, and one of the nuts to the washer. A total of four such details will be required.
After this, the washers are welded to the segments of the round pipe (on both sides). You do not need to unscrew the bolt - so that the welding does not get into the thread.
As a result, we got two homemade bushings (40 mm and 60 mm long) with internal thread. We clean them using angle grinders.
Next, from the piece of the strip, two pieces of 35 cm long will need to be cut. On another piece of the strip, the author marks two pieces of 5 cm long.
Next, you need to find the center of the strip and drill a hole between the segments using a metal crown with a diameter of 20 mm.
Fasting, cut the marked section of the strip in half and get two details. They need to be sanded a little for a snug fit to the round pipe.
Then we mark the center on the profile pipe, weld to it the previously manufactured two parts, and to them - a sleeve 60 mm long.
Machine manufacturing process
On metal strips that were previously trimmed, the author marks the places where holes were drilled.
We retreat from the edge of the strip 2 cm, then make markings in increments of 7 cm. We drill holes with a diameter of 10 mm.
The author uses a step drill for this - very convenient. Next, you will need to fasten the strip to the sleeve using the M10 bolts.
To the end of the strips (from the end, from the bottom and from the top), the author welds small pieces of metal, and to them - a piece of a round pipe.
Next, bend the arc from the strip and cut it in half. We weld one of the halves to the corners. We reinforce the structure using pieces of reinforcement or a square.
We recommend reading: a home-made bending machine from improvised materials.
Then you need to weld a piece of the corner to it, which will be used as a stop, and drill one hole with a diameter of 8 mm in it. A nut must be welded to it.
A bolt is screwed into the nut, to which the author welds a handle from a piece of round bar.
At the last stage, we drill mounting holes and proceed directly to the assembly of the entire structure.
For details on how to make a home-made manual machine for bending metal blanks, see the video on our website.